Road works
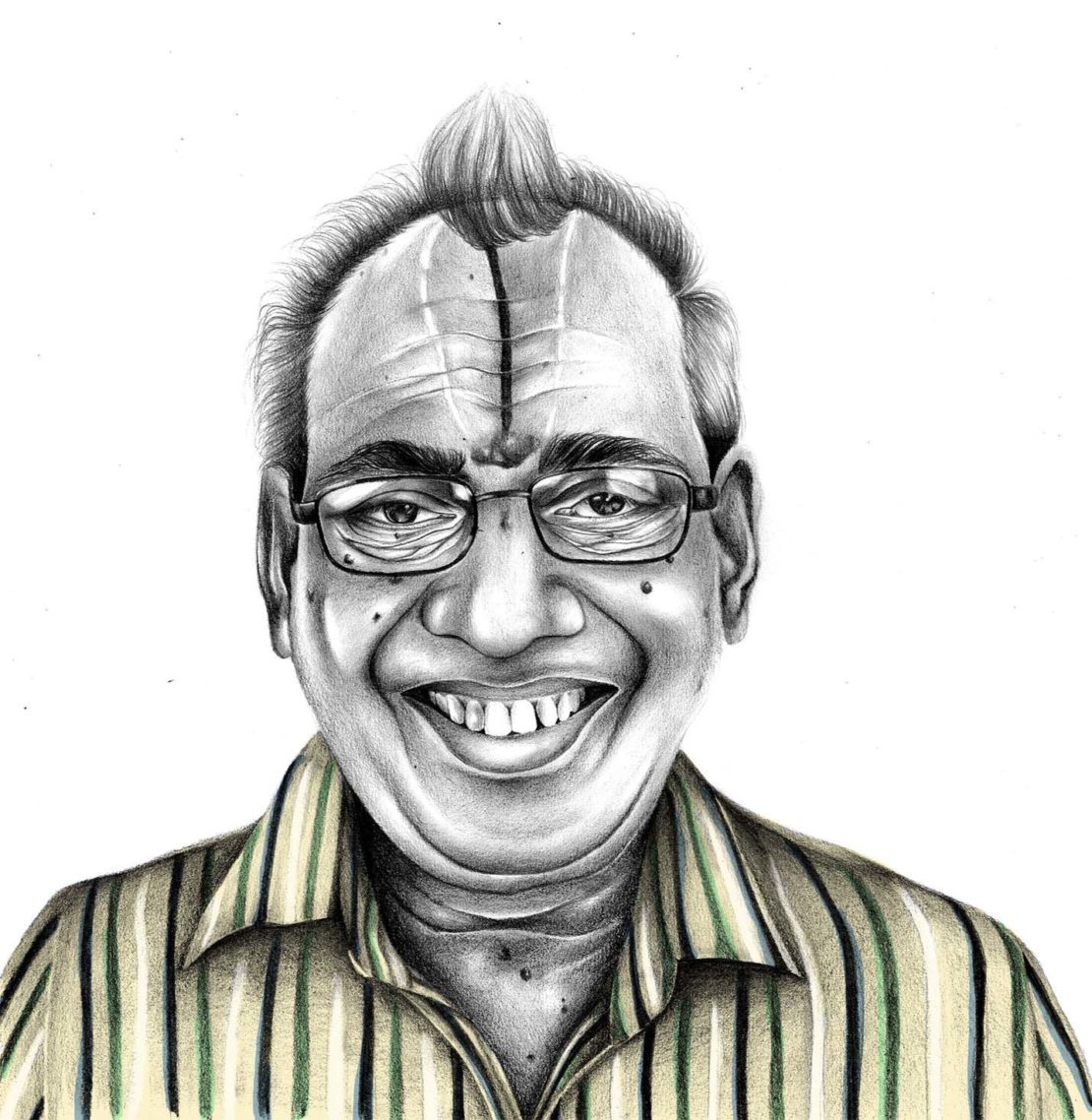
Who?
A chemistry professor at the Thiagarajar College of Engineering, near Madurai, India, who developed a technique for transforming waste plastic into an ingredient for new roads – as a partial substitute to tar.
Why?
It helps tackle India’s enormous, and worsening, rubbish problem – much of it is non-recyclable plastic waste – while making for cheaper roads. They’re better, too: the roads are stronger and more resistant to water, heat and pressure than a normal stone and tar mix.
How?
The method is simple and doesn’t substantially change the road-laying process, making it easy to adopt anywhere. But it takes a lot of plastic: for 1km of road, you need 1 tonne of waste plastic (about a million carrier bags) for 9 tonnes of bitumen (tar). One substantial advantage is that there’s no need to sort or segregate different kinds: nearly all plastic, from supermarket bags to thick PET bottles or multi-layered packaging, can be used as it comes. A mix of gravel, shredded plastic and bitumen is baked at 150C so that it melts and then spread as normal.
What's next?
Vasudevan developed and patented the process in 2006, and more than 3,000 miles of Indian roads have been paved with plastic since. More recently, Vasudevan created monoblocks from waste plastic that could replace traditional bricks.